Loading...
Model: YGCB
Tractive flow divider-combiner assembly
Capacity:
See CAD Files tab below to request images.
Function
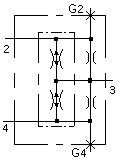
Technical specifications
Modifiers
Ports
- A, A/SPorts 2, 3, 4: 1/4" NPTF; Gage Ports (Plugged): SAE 4;
- B, B/SPorts 2, 3, 4: 3/8" NPTF; Gage Ports (Plugged): SAE 4;
- C, C/SPorts 2, 3, 4: 1/2" NPTF; Gage Ports (Plugged): SAE 6;
- I, I/SPorts 2, 3, 4: SAE 6; Gage Ports (Plugged): SAE 4;
- J, J/SPorts 2, 3, 4: SAE 8; Gage Ports (Plugged): SAE 4;
- K, K/SPorts 2, 3, 4: SAE 10; Gage Ports (Plugged): SAE 4;
- T, T/SPorts 2, 3, 4: 1/4" BSPP; Gage Ports (Plugged): SAE 4;
- U, U/SPorts 2, 3, 4: 3/8" BSPP; Gage Ports (Plugged): SAE 4;
- V, V/SPorts 2, 3, 4: 1/2" BSPP; Gage Ports (Plugged): SAE 4;
This valve assembly is intended for use in tractive systems. It incorporates a divider/combiner valve along with provisions for slip orifices. The divider/combiner provides 2 equal flows for positive traction and the slip orifices can be sized to allow for steering.
- Operating characteristics cause the leg of the circuit with the greatest load to receive the higher percentage of flow in dividing mode. If a rigid mechanism is used to tie actuators together, the lead actuator may pull the lagging actuator and cause it to cavitate.
- In combining mode, compensating characteristics will cause the leg of the circuit with the lowest load to receive the higher percentage of flow. If a synchronization feature is not included, an additive accuracy error will be experienced with each full stroke of the actuator.
- In applications involving rigid mechanisms between multiple actuators, operating inaccuracy will cause the eventual lock-up of the system. If the mechanical structure does not allow for the operating inaccuracy inherent in the valve, damage may occur.
- In motor circuits, rigid frames or mechanisms that tie motors together, and/or complete mechanical synchronized motion of the output shaft of the motors, either by wheels to the pavement or sprockets to conveyors, will contribute to cavitation, lock-up and/or pressure intensification.
- Variations in speed and lock-up can be attributed to differences in motor displacement, motor leakage, wheel diameter variance and friction of wheels on the driving surface.
- Extreme pressure intensification can occur on multiple wheel drive vehicles.
- Differential slip for tractive drive systems must be achieved with orifices in the body/manifold.
- Below the minimum flow rating there is not enough flow for the valve to modulate. It is effectively a tee. If flow starts at zero and rises, there will be no dividing or combining control until the flow reaches the minimum rating.
- Body TypeLine mount
- Capacity2 - 9 gpm
- Mounting Hole Diameter.34 in.
- Mounting Hole DepthThrough
- Mounting Hole Quantity2
Why doesn't Sun anodize their aluminum bodies?
How big is a drop of hydraulic oil?
Direct acting or pilot operated - what do I use?
- Important: Carefully consider the maximum system pressure. The pressure rating of the manifold is dependent on the manifold material, with the port type/size a secondary consideration. Manifolds constructed of aluminum are not rated for pressures higher than 3000 psi (210 bar), regardless of the port type/size specified.
- For detailed information regarding the cartridges contained in this assembly, click on the models codes shown in the Included Components tab.
Highlights
Technical Tips
Technical Information